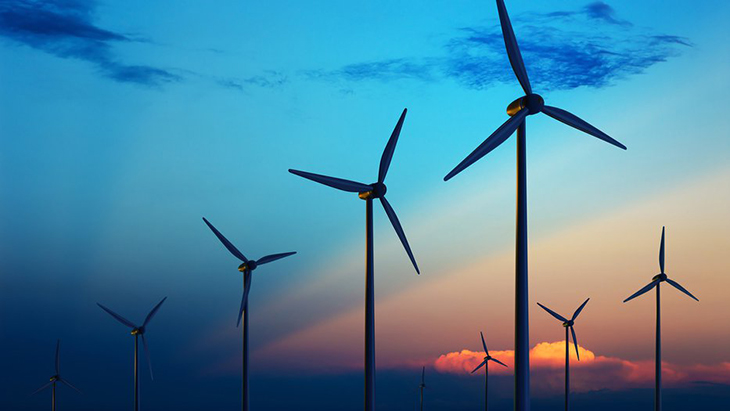
As the first generation of wind turbines nears the end of its operational life, the issue of what to do with the colossal fiberglass blades has become a pressing concern for an industry that prides itself on being environmentally friendly and sustainable.
While it’s true that wind turbines don’t rely on fossil fuels to generate electricity, the accumulation of non-recyclable fiberglass blades in landfills is projected to exceed 40 million tons over the next two decades.
However, some forward-thinking companies are tackling this problem from a different perspective. One such company is REGEN Fiber, a subsidiary of the trucking company Tavero. They envision a future where decommissioned wind turbine blades are repurposed rather than discarded, and their solution involves incorporating these blades into concrete and asphalt.
Their primary output is a high-performance reinforcement fiber that significantly enhances the strength and overall durability of various concrete and mortar applications, including pavements, slabs-on-grade, and precast products. Additionally, REGEN Fiber produces microfibers and additives derived from wind blade components for use in various composite materials, concrete mixes, and soil stabilization applications.
By diverting decommissioned wind turbine blades away from landfills and preventing the release of combustion byproducts like carbon into the atmosphere, REGEN Fiber is pioneering a sustainable solution to address the wind industry’s growing challenge of environmentally responsible wind turbine component disposal.
“With tremendous growth projected in the wind industry and an increasing number of turbines already reaching the end of their approximately 20-year lifespan, REGEN Fiber is entering the market at the perfect time,” Jeff Woods, director of business development at Travero, mentioned in a statement he recently made.
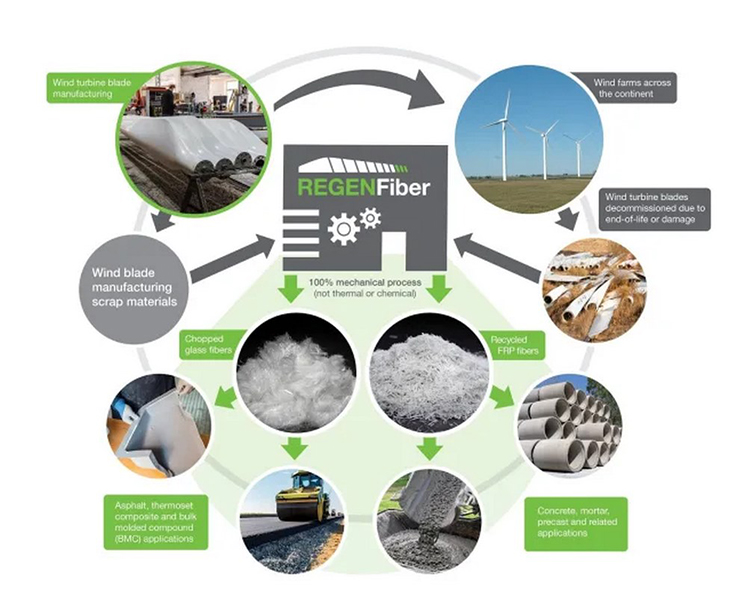
“Recycling blades without using heat or chemicals while simultaneously keeping them out of landfills or being burned supports the sustainability goals of both the wind industry and customers receiving the recycled products.”
In the latter half of 2023, significant large-scale recycling operations for decommissioned wind turbine blades are slated to commence. Construction of a state-of-the-art REGEN Fiber manufacturing facility, dedicated to the recycling of retired blades, is presently underway in Fairfax, Iowa.
Once the full-scale operations in Fairfax reach their peak production capacity, REGEN Fiber envisions the recycling of more than 30,000 tons annually of shredded blade materials and byproducts stemming from the production of new blades.
A promising avenue for repurposing non-recyclable products is their integration into reinforcing concrete, asphalt, and various paving materials.
During the COVID pandemic, the proliferation of mask production raised concerns regarding their lack of recyclability. Notably, the Royal Melbourne Institute of Technology and Melbourne Technical College devised a solution by incorporating discarded masks into the composition of road asphalt mixtures. A mere one kilometer of road can consume up to 3 million masks.
In a similar vein to masks, baby diapers pose challenges for recycling. Scientists at the School of Environmental Engineering at the University of Kitakyushu in Japan, however, have devised a method to replace 40% of the sand in concrete mixtures with shredded baby diapers.
What are your thoughts? Please comment below and share this news!
True Activist / Report a typo