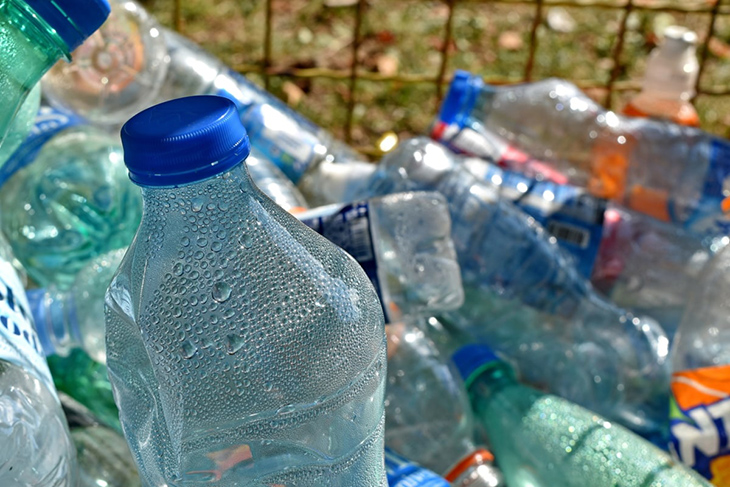
They say that the toughest part of the tree is not the trunk. Neither is it the roots. While it may seem unbelievable, the walls of its microscopic cells are actually the strongest portion.
In fact, one wood cell wall is made from fibers of cellulose. This is an abundant polymer that’s found in nature. This is also the main structural component found in all plants and algae.
Within each fiber of the cellulose are reinforcing cellulose nanocrystals. This is otherwise known as CNCs. These chains of organic polymers are arranged in almost perfect crystal patterns. If you took a look at these in nanoscale, CNCs are, in reality, stronger and stiffer than Kevlar. Hence, scientists thought that if the crystals could be placed into a variety of materials in significant fractions, CNCs could be the perfect solution to stronger, more sustainable, naturally derived plastics. This could mean so much, especially in terms of going green.
A team of researchers and experts from MIT have been inspired to delve deeper into this matter. They engineered a composite material that’s made mostly from cellulose nanocrystals and mixed with a smidgeon of synthetic polymer. In terms of specific numbers, these organic crystals take up about 60 to 90 percent of the material. This has been the highest fraction ever of CNCs achieved in a composite.
The researchers discovered how the cellulose-based composite is actually sturdier and tougher than some types of bone. It’s also harder than those typical aluminum alloys that you may be familiar with. The material comes with a brick-and-mortar microstructure. It’s very much like nacre, which is the hard inner shell lining of some mollusks.
The team was able to come up with the perfect recipe for the CNC-based composite. They were able to fabricate this with the use of both 3D printing and traditional casting methods. They printed and cast the composite into pieces of film that are about the size of a penny. Then, they used these newly created materials to test out its strength and hardness. They also used a machine to form the composite into the shape of a tooth. This could be an important step in dentistry because the new material might just be used to make cellulose-based dental implants one day. Or, they could also utilize these for plastic products that are stronger, tougher, and more importantly, very sustainable.
“By creating composites with CNCs at high loading, we can give polymer-based materials mechanical properties they never had before,” said A. John Hart. He is a professor of mechanical engineering. He added, “If we can replace some petroleum-based plastic with naturally-derived cellulose, that’s arguably better for the planet as well.”
Gel Bonds
In every single year, more than 10 billion tons of cellulose is synthesized from the bark, wood, or leaves that come from plants. Most of it goes to the manufacturing of paper and textiles. Then, some of them would be processed into powder for food thickeners and cosmetics.
But just recently, scientists have also looked into the variety of uses for cellulose nanocrystals. These can be extricated from cellulose fibers through a process called acid hydrolysis. The extremely and uniquely sturdy crystals could be then be used as natural reinforcements in polymer-based materials. At this point in time, however, researchers have only been able to assimilate low fractions of CNCs because the crystals tend to clump and only weakly bond with the polymer molecules.
Of course, Hart and his colleagues looked into developing a composite that comes with a higher fraction of CNCs. They wanted to shape these new materials into something strong and durable. This was made possible because they began by mixing a solution of synthetic polymer with CNC powder that’s available in commercial markets. They then set out to determine the proper ratio of CNC and polymer that would create a gel from the solution, cone that has the consistency that could either be shot into the nozzle of a 3-D printer or poured into a mold for casting. They made use of an ultrasonic probe to break the clumps of cellulose that may form in the gel. Thus, this cellulose would be easier for dispersal and to form strong bonds with polymer molecules.
They fed a portion of the gel they made through a 3-D printer. The rest were poured into a mold that they would later cast. The printed samples were then set out to dry. During the entire process, they found that the material shrank and it left a solid composite that’s made primarily of cellulose nanocrystals.
“We basically deconstructed wood, and reconstructed it,” Rao said. “We took the best components of wood, which is cellulose nanocrystals, and reconstructed them to achieve a new composite material.”
Tough Cracks
Interestingly enough, the outcome was unexpected. The team behind the design went to examine the composite’s structure by placing it under a microscope. They then noticed how the grains of cellulose settled and formed into a brick-and-mortar pattern, which is very much like a nacre. In nacre, this zig-zagging microstructure hinders cracks that form from piercing straight through the material. This was the very same case for the new cellulose composite.
They set out to test and experiment how the new material is able to resist cracks. They used a variety of tools to initiate first nano- and then micro-scale cracks. They found that even across a myriad of scales, the composite’s arrangement of cellulose grains still hindered the cracks that form from splitting the material inside. This resistance to plastic deformation makes the composite hard and stiff, its quality straddling the boundary between conventional plastics and metals.
As for the future, the team wants to look for ways to lessen the shrinkage of gels during the drying process. While this doesn’t pose much of an issue when it comes to printing small objects, anything larger could give way and crack as it dries.
“If you could avoid shrinkage, you could keep scaling up, maybe to the meter scale,” Rao said. “Then, if we were to dream big, we could replace a significant fraction of plastics, with cellulose composites.”
The results of the project have been published in the journal Cellulose.
What are your thoughts? Please comment below and share this news!
True Activist / Report a typo