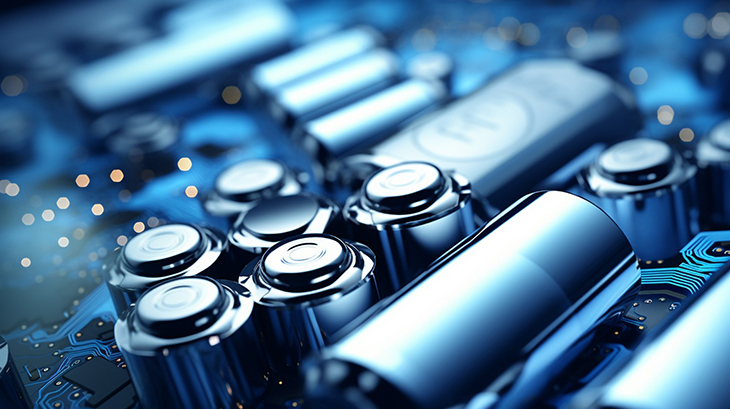
According to a group of Swedish scientists, they have devised an innovative battery recycling technique specifically tailored for electric vehicle batteries, enabling the reclamation of 100% of aluminum and 98% of lithium content.
The experts at Chalmers University of Technology have introduced an effective approach to extract metals from depleted batteries while simultaneously reducing the depletion of precious resources like nickel, cobalt, and manganese.
Remarkably, this process does not necessitate costly or hazardous chemicals; instead, the researchers employ oxalic acid, an organic acid readily available in the plant kingdom.
“So far, no one has managed to find exactly the right conditions for separating this much lithium using oxalic acid, whilst also removing all the aluminum,” Léa Rouquette said. She’s aPhD student in the Department of Chemistry and Chemical Engineering. “Since all batteries contain aluminum, we need to be able to remove it without losing the other metals.”
In the battery recycling lab at Chalmers University, Rouquette and research leader Martina Petranikova demonstrated their innovative method. They showcased the process of transforming pulverized components into a finely ground black powder, which was then dissolved in a transparent liquid — oxalic acid.
Rouquette created both the powder and the liquid using a setup akin to a kitchen mixer. Despite its seemingly simple appearance, the procedure represents a significant scientific breakthrough. Through meticulous adjustments of temperature, concentration, and time, the researchers developed a novel approach using oxalic acid, an environmentally friendly substance naturally found in plants like rhubarb and spinach.
“We need alternatives to inorganic chemicals. One of the biggest bottlenecks in today’s processes is removing residual materials like aluminum,” says Martina Petranikova. She’s an Associate Professor at the Department of Chemistry and Chemical Engineering at Chalmers. “This is an innovative method that can offer the recycling industry new alternatives and help solve problems that hinder development.”

The recycling technique involving water, known as hydrometallurgy, typically dissolves all metals in an electric vehicle (EV) battery cell using an inorganic acid in traditional processes. Subsequently, impurities like aluminum and copper are eliminated, and valuable metals like cobalt, nickel, manganese, and lithium are recovered separately. Despite the small amount of remaining aluminum and copper, several purification steps are necessary, each of which can result in the loss of lithium.
In the innovative approach, researchers have reversed the sequence, first recovering lithium and aluminum. This change minimizes the wastage of precious metals essential for manufacturing new batteries.
In the latter part of the procedure, akin to brewing coffee, a black mixture is filtered. During this process, aluminum and lithium end up in the liquid, while other metals are retained in the solids. The subsequent step involves separating aluminum and lithium.
“Since the metals have very different properties, we don’t think it’ll be hard to separate them. Our method is a promising new route for battery recycling – a route that definitely warrants further exploration,” says Rouquette. Her published results are found in the journal Separation and Purification Technology.
Petranikova’s research team actively collaborates with companies to advance electric car battery recycling efforts and participates as a key partner in significant research and development initiatives like Volvo Cars’ and Northvolt’s Nybat project. Funding for this research comes from sources such as the Swedish Energy Agency, BASE Batteries Sweden, and Vinnova.
What are your thoughts? Please comment below and share this news!
True Activist / Report a typo